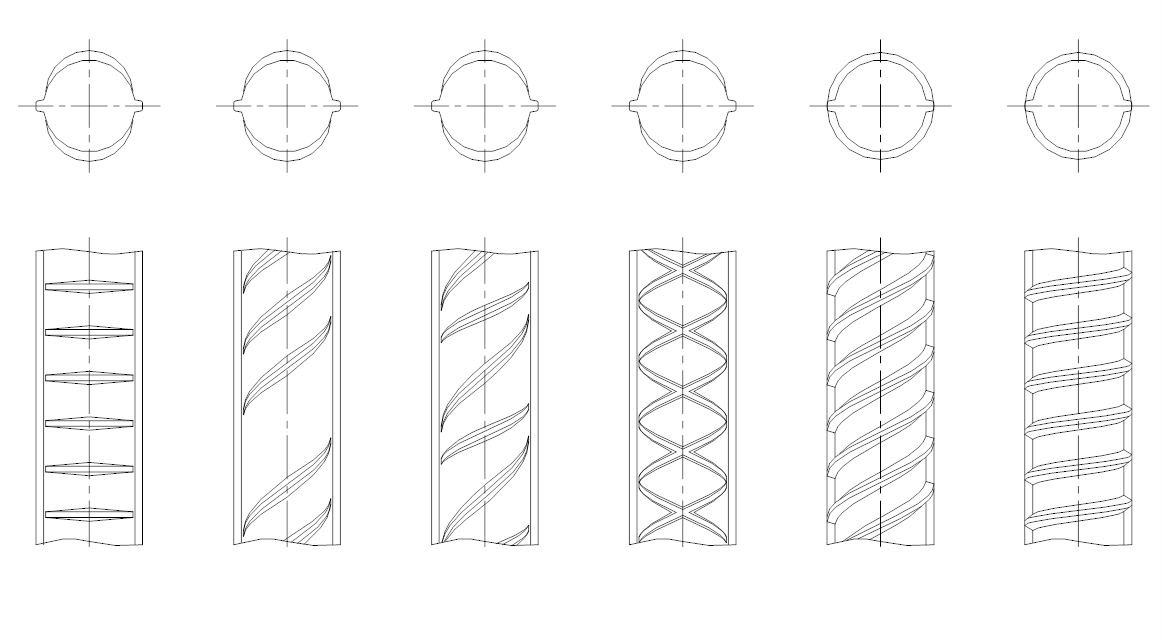
XK500G CNC notch milling machine installed with Seimens808D (4 axis server motor and 1 spindle VFD), suitable for tungsten carbide roll or high speed steel roll or high-nickel-chromium composited roll, or cast iron roll.
It can notch ribs mark the symbol on the roll. The roll size: Max Diameter:500mm; Max length :2500mm; Max workpiece weight:2500Kg. Bar Size:6~50mm.
XK500G CNC notch milling machine have 2 guideway. Notching tooling and marking cutter are mounted side by side on the same side of the CNC machine;. Two guideway for tailstock; two guide ways for saddle. The guideway lubricate by auto-lubrication pump. There have an AC for electrical cabinet.
XK500G CNC notch milling machine can be used for following functions:
Function 1: notch (base function)
CNC machine can notch ribs for the deformed steel bar with all standard. The CNC machine use 4 server motors
X axis :notch tool feed forward or turn back.
Y axis: the roll turning with worn gear
Z axis : notching tool turning on the lever surface with gear drive.
A axis: the notch tool move from the left to the ringt.
Function 2: marking ( optional function)
CNC machine can mark logo, character, drawings etc. on the surface of the roll.
Marking cutter feed forward or turn back, and move from the left to the right
X axis :notch tool feed forward or turn back.
Y axis: the roll turning with worn gear
Z axis: the notch tool move from the left to the ringt.
A axis: the notch tool move from the left to the ringt.
S axis: the marking cutter spindle turning with high speed, VFD
XK500G CNC notch milling machine, with its sophisticated software package and represents a complete notching and marking unit able to answer at the challenges of the new demanding re-bar market. Some advantages of the package we propose are the following:
- FLEXIBILITY
The machine can perform automatically all the international standards and whatever is required in terms of notch skipping and notch enlarging.
- ACCURACY
Absolute accuracy for the notch dimensions (rib depth, thickness and angle), and tool positioning is achieved by the special unique direct motor-tool transmission with no belts. That's particularly important when performing Tungsten Carbide rings and composite rolls. The worker input the diameter of the roller; the rib depth; angle; etc. then the CNC will run automatically.
- AUTOMATIC TOOL POSITIONING
Tool can move to the next pass automatically, the worker only need input the distance which between the two pass. So it’s positioning is a quick, accurate and automatic operation
- EASY RECODINTIONING
The Y axis and Z axis have zero point function. The machine can find the this zero point easy. So in the roll reconditioning operations, the tool can be easily and accurately centred on the worn rib
- OPERATOR TIME REDUCTION
Machine can perform automatically all the operations like skipping and enlarging ribs, as well as the change of channel. That means a fantastic reduction in the operator time. - NOTCHING AND MARKING IN THE SAME MACHINE
The machine can make logo on the roller.
The logo making milling cutter can move forward or back.
- very easy to find the restart point
The CNC can easy to find the restart point after power loss. This function can grant the continuity of your job in every circumstance. In case of power loss, black-outs or machine resetting, the programmed cycle can re-start exactly from the point where it was interrupted simply with a click. - EASY TO USE
We make the special software, everything is driven by the program to assure correct data inputting and machine programming. The worker only input the parameters such as the diameter of roller; The radius of the pass; the number of the ribs ; the depth of the ribs; where to skip the ribs;
- Cutter protection
The tooling feed with the equal feed depth. The cutter will bear the force more and more while the cutter feed forward.
The tooling feed with the same force, it’s very good for improving the cutter life, and for improving surface quality and reduce the machining time. Working area and removed material are much more constant to reduce machining time
- capacity
CAPACITY |
|
Maximum roll diameter mm |
500 |
Minimum roll diameter mm |
100 |
Maximum roll length mm |
2500 |
Maximum roll weight Kg |
2500 |
Notching rebar diameter range mm |
6-50 |
Tooling spindle speed inclined notches rpm |
0-500 |
Notching per roll |
As many as required |
Notching angle |
free choice |
Omitting ribs |
free choice |
Enlarging ribs |
free choice |
The bed width mm |
580 |
The diameter of chuck( 4 jaws) mm |
400 |
The spindle tape hole |
Ms5 |
Tailstock guill diameter mm |
180 |
Tailstock tape hole |
Ms5 |
Machine dimensions(LWH) mm |
5600*1600*1850 |
Weight Kg |
5500 |
Machine can execute ribs according to all international standards |
11.CNC controller
CONTROL |
|
CNC Control |
Siemens808D |
Remote hand wheel |
|
CF card |
- Server Equipment
EQUIPMENT |
Working system : 4 axis CNC digital controlled |
Work piece Y axis, controlled by Siemens digital motor Kw3.5 |
Tooling Z axis, controlled by Siemens digital motor Kw 2.5 |
Longitudinal feed (A axis), controlled by Siemens digital motor Kw 1 |
Tooling cross feed spindle (X axis), controlled by Siemens digital motor Kw 1 |
Logo making cutter milling spindle (S spindle axis) 2.2kw;VFD |
Tailstock |
Fixed center complete of extracting holes |
Four jaw chuck |